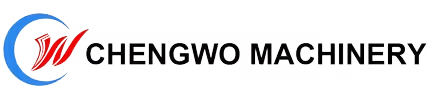
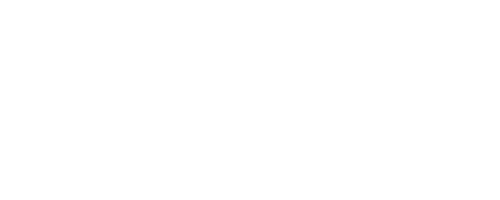
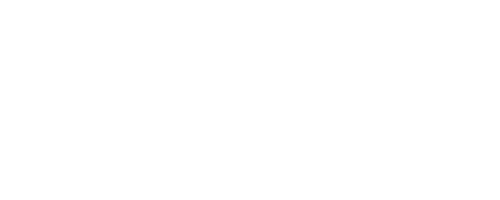
This article explores innovative food extrusion machine solutions that are driving efficiency and customization in the food processing industry.
In the dynamic landscape of food manufacturing, staying competitive demands innovation, adaptability, and precision. One technology that has become a cornerstone of modern food processing is the food extrusion machine. From snack foods and cereals to pet food and meat substitutes, extrusion technology is transforming the way food is produced. Chengwo Food Machinery, an industry leader with a deep-rooted engineering R&D center, is setting new benchmarks by integrating modular design and intelligent automation into extrusion machinery. This article explores innovative food extrusion machine solutions that are driving efficiency and customization in the food processing industry.
A food extrusion machine is a complex piece of industrial equipment designed to shape, cook, and texturize food products by forcing them through a specially designed die. The process combines several functions—mixing, heating, shearing, and forming—into a continuous and controlled operation. These machines are widely used across various sectors, including snack production, cereal manufacturing, pet food, and alternative protein processing.
The food extrusion process allows for a high degree of customization in shape, size, texture, and even nutritional composition. Thanks to automation and intelligent control systems, modern machines are now capable of delivering consistent quality with minimal human intervention.
Food extrusion machines operate continuously, significantly reducing downtime and increasing throughput. The modular designs pioneered by Chengwo Food Machinery allow for quick reconfiguration, enabling manufacturers to switch product lines with ease.
These machines can handle a variety of ingredients, from starches and proteins to fibers and fats. This versatility supports the production of diverse items like puffed snacks, textured vegetable proteins (TVP), and fortified cereals.
With automated monitoring and control, extrusion technology ensures that each product meets strict quality standards. Parameters such as temperature, moisture, and pressure are finely tuned to achieve the desired characteristics.
The extrusion process consolidates several production stages into a single step, resulting in energy savings and reduced labor costs. Furthermore, the high throughput of a food extrusion machine leads to faster return on investment.
Understanding the structure of a food extrusion machine can offer deeper insights into its functionality. Below are the essential components that contribute to its effectiveness:
Extruded snacks such as puffed corn sticks, cheese balls, and rice crackers are staples in the global snack industry. A food extrusion machine can efficiently produce these in various shapes and flavors.
From flakes to rings and multi-grain clusters, extrusion machines support a wide array of cereal products. The integration of modular design allows producers to switch between formats rapidly.
Plant-based proteins processed through extrusion replicate the texture and appearance of meat. This application is critical in meeting the rising demand for sustainable and vegan-friendly products.
The pet food industry benefits from extrusion technology to create dry kibble with consistent texture and nutritional profiles, ensuring pet health and customer satisfaction.
Food extrusion machines are also employed in manufacturing functional foods enriched with vitamins, minerals, and dietary fiber, helping meet health-conscious consumer trends.
Feature/Function | Description | Benefit |
---|---|---|
Modular Design | Interchangeable components for quick setup | Flexibility for different product lines |
Automated Control Systems | Real-time monitoring of temperature, pressure, and moisture | Consistency and reduced need for manual intervention |
High Throughput | Capable of continuous, high-volume production | Lower per-unit cost |
Energy Efficiency | Combines multiple operations in a single machine | Reduced energy consumption and operational costs |
Hygienic Construction | Stainless steel build and easy-to-clean design | Compliance with food safety standards |
Versatile Die Options | Variety of shapes and sizes available | Customization for market differentiation |
Integrated Preconditioner | Prepares raw materials before extrusion | Improves texture and product expansion |
Chengwo Food Machinery is not just a manufacturer; it is a solutions provider. With a dedicated engineering and R&D center, the company has been at the forefront of modularization in extrusion technology. Key advantages include:
The food industry is evolving rapidly, and extrusion technology is evolving with it. Key future trends include:
The integration of smart technologies and IoT (Internet of Things) into food extrusion machines is transforming production environments into intelligent systems. These advancements allow real-time data collection, remote diagnostics, and predictive maintenance. Operators can monitor temperature, moisture, and pressure with precision, reducing human error and downtime. As a result, manufacturers achieve greater consistency, efficiency, and traceability across the production line.
Sustainability is no longer optional—it’s a driving force in food production. Extrusion machines are evolving to reduce energy consumption and minimize waste. New designs optimize thermal efficiency and material usage, enabling processors to work with upcycled ingredients and alternative proteins that reduce environmental impact. Water reuse systems and recyclable materials in machine construction further enhance ecological responsibility.
Combining food extrusion with 3D printing opens a new frontier in personalized and on-demand food production. This technology allows for the creation of intricate shapes, customized nutrition, and visually appealing meals, especially useful in hospitals, schools, and space missions. With precise extrusion control, 3D food printing can accommodate dietary restrictions and deliver tailored textures for specific audiences like elderly or medical patients.
As global demand for alternative proteins increases, extrusion technology is key to processing novel sources like insect protein, algae, fungi, and lab-grown meat. These ingredients often require unique handling and texturization methods that extrusion machines are being specifically adapted for. The resulting products replicate the fibrous structure of traditional meat, offering a sustainable and ethical protein solution for the future.
Food extrusion machines are revolutionizing how food is produced—enhancing efficiency, consistency, and product innovation. Whether you’re producing snacks, cereals, or cutting-edge plant-based foods, extrusion technology offers unmatched value and scalability. Chengwo Food Machinery leads the way with its modular, intelligent, and high-performance food extrusion machine solutions.
Looking to transform your food production capabilities? Contact us today to explore how our extrusion solutions can power your success.
What types of food can be made with a food extrusion machine?
A food extrusion machine can produce a wide range of products such as puffed snacks, ready-to-eat cereals, protein bars, pasta, pet food, and plant-based meat analogs. The versatility of extrusion technology allows processors to use various raw materials including grains, legumes, and protein isolates. By adjusting machine settings and die configurations, different shapes, textures, and densities can be achieved. This flexibility makes it suitable for both staple foods and high-value functional products.
Is extrusion safe for food products?
Yes, extrusion is a highly safe and controlled process commonly used in the food industry. It involves high-temperature short-time (HTST) processing, which effectively destroys harmful pathogens and microorganisms without significantly degrading nutrients. The enclosed and continuous nature of the process minimizes the risk of contamination. Additionally, modern food extrusion machines comply with strict food safety standards such as HACCP and GMP.
How much space does a typical extrusion line require?
The space requirement depends on the model, production capacity, and degree of automation. A small to mid-scale line may occupy around 50–100 square meters, while large-scale industrial lines could require over 300 square meters. Modular designs offered by Chengwo Food Machinery allow for customized layouts to fit various factory footprints. Proper planning ensures smooth workflow, efficient material handling, and easy maintenance access.
What maintenance is needed?
Regular maintenance includes cleaning the extruder barrel and screws, lubricating moving parts, checking die and cutter wear, and inspecting sensors and control systems. Scheduled maintenance minimizes unexpected downtime and extends machine lifespan. Chengwo provides detailed manuals, training programs, and on-site support to help clients establish efficient maintenance routines. Predictive maintenance technologies can also be integrated for better performance tracking.